Seratech featured in Construction Management
Low-carbon concrete: separating greenwash from reality
By Kristina Smith
2/6/20232 min read
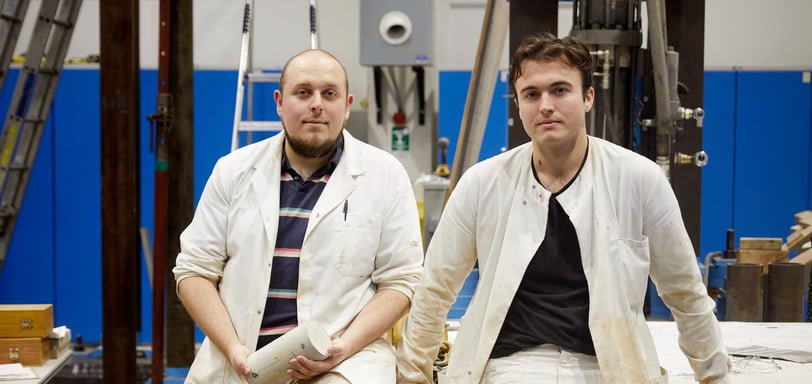
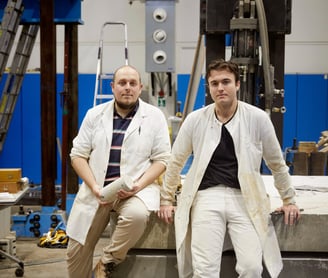
It took the Covid lockdown for Imperial College London researchers Sam Draper and Barney Shanks to find time to talk to each other about their research projects. When they did, an amazing opportunity emerged.
“Sam spotted this silica material I am working on and asked whether it worked in normal cement,” recalls Shanks. That was back in November 2020. Today the pair, working in their company Seratech, which they founded in 2021, have found a way to produce zero-carbon concrete.
At the time of the initial conversation, Shanks was working on a magnesium-based cement derived from olivine, a magnesium silicate mineral. His PhD was investigating how the commonly occurring material could be used for concrete, splitting it into magnesium and silica and then recombining them with water to form a new bonding phase similar to cement, but without carbon dioxide being created.
Magnesium-based cements are in their infancy and don’t work well enough yet to be interesting to industry, says Shanks. However, they found a way of combining the two separated elements Shanks was producing with carbon dioxide to create a cement replacement material similar to fly ash.
“Because the magnesium component is very reactive, we don’t have to purify or liquify the carbon dioxide, we just take it directly from flues and pass it over the magnesium to form magnesium carbonate.”
Replacement mixes
Shanks and Draper then experimented with a couple of mixes, replacing 20% and 35% of the cement with the new material, to correspond to CEM IIA and CEM IIB cements. Due to the carbon sequestered, the 35% replacement mix leads to zero-carbon concrete.
And it performs well too, says Draper: “It has good compressive strength performance, 40MPa-plus,” he says. “It’s stronger than the fly ash mix and getting close to CEM I in strength. Its early-age strength is good too because the silica is very reactive.”
The potential of the Seratech process, which is currently progressing through the patenting process, has already been recognised. It has won awards and attracted grant funding.
The next step is to transform the laboratory process into something that can be applied to cement plants.
The goal is to create a system that can be easily retrofitted to any cement plant, or to another process that produced carbon dioxide, such as steel manufacture or energy production. If all goes to plan, they could have a pilot facility in operation in late 2023 or early 2024.
Early this year, the company plans to scale up production to allow more comprehensive testing. “After that we would look to do a couple of carefully selected pilot projects,” says Draper.
For the original article, click here