Seratech in ArchDaily.com
“Achieving Sustainable Construction Is First Using the Right Material for the Right Job”: In Conversation With Seratech
By Paul Yakubu
10/10/20233 min read
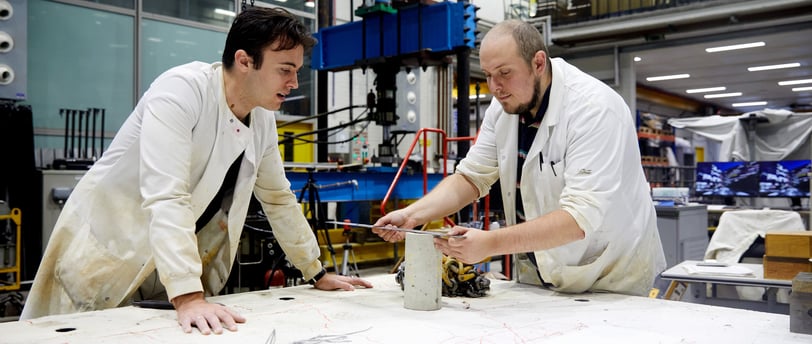
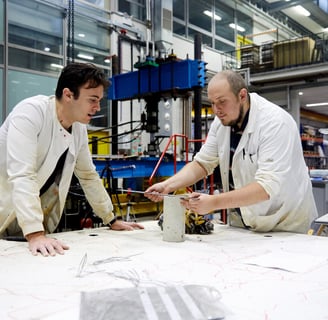
Seratech's technology, developed by Sam Draper and Barney Shanks, eliminates the CO₂ footprint of concrete and reduces carbon emissions in construction. This innovative process uses silica, a waste product from flue gases, as a carbon-negative cement replacement in concrete. By incorporating silica, the required amount of Portland cement is reduced by 40%, resulting in the production of carbon-negative concrete. This groundbreaking technology won the 2022 Obel Award for its focus on embodied emissions.
The Obel Award is an international award that promotes architecture in the service of both people and the planet. Seratech was the fourth winner of this new international prize for architectural achievement, preceding this year's 'Living Breakwaters' by SCAPE Landscape Architecture. ArchDaily had the chance to interview Sam Draper, CEO of Seratech, about the company's role in building a sustainable construction industry and their plans for scaling their innovative process.
ArchDaily (Paul Yakubu): Concrete, as a material, currently dominates the built environment. How can we transition away from it to create a sustainable and durable future?
Seratech (Sam Draper): One of the most effective routes for specifiers to decarbonize the built environment is to ensure that they are using the right material for the right job. Some concrete structures, such as low-rise buildings, can easily be replaced by materials such as timber. However, there are many applications where concrete is the most suitable material, including foundations, tunnels, and other large infrastructure products.
Minimizing cement and concrete consumption is an important first step to decarbonize the built environment, and relieves some of the demand on cement replacement materials, like GGBS (a by-product of the steel industry). Beyond this, novel alternatives, such as Seratech’s, will be vital to reach net zero.
AD: What inspired the production of a carbon-negative cement replacement material (silica) and what are its applications in concrete?
ST: Seratech’s founders, Sam Draper and Barney Shanks, met whilst studying PhDs at Imperial College London, researching sustainable cement. The driver behind Seratech was to deliver an industry-focussed sustainable cement technology that can be implemented without massive deviations from existing construction practices.
Seratech utilizes carbon capture, mineralization, and utilization (CCMU) to turn naturally abundant magnesium silicates into cement replacement materials, permanently sequestering CO2 within them. The chemistry of these materials is almost identical to that of existing materials such as GGBS and fly ash. This approach means the concretes are suitable for all applications, including products, pre-cast, and ready-mix.
The aim is for humanity to be able to continue building robust cities and infrastructure, but without the climate cost of traditional cement mixes and with the Seratech technology this goal is achievable!
AD: In terms of structural capacity and durability, how does Seratech's innovative material compare to traditional concrete?
ST: Seratech’s cement replacement material is chemically similar to other widely used alternatives, such as GGBS and fly ash, with a high content of amorphous silica. This makes it very reactive and offers good structural performance and durability, even at early ages, ensuring there is no delay to construction programs by using the material. To date, we have prepared concretes with 40% of the Portland Cement replaced by our Silica which displays higher compressive strengths from 3 days onwards than the equivalent CEM I concrete.
AD: How does Seratech plan to scale this innovation in the built environment?
ST: Seratech is currently in the process of designing and procuring a Pilot facility that will allow us to manufacture our materials at a scale of tonnes per week. The resulting materials will be used in a range of projects with major developers, structural engineers, and contractors to demonstrate the performance and the potential of the materials.
Once the process and products are proven at scale, Seratech will pursue a licensing model to grow the adoption of the technology as quickly as possible and maximize the potential emissions reduction.