Seratech in Build in Digital - Can Concrete Ever Come Clean?
By Tim Clark
7/22/20246 min read
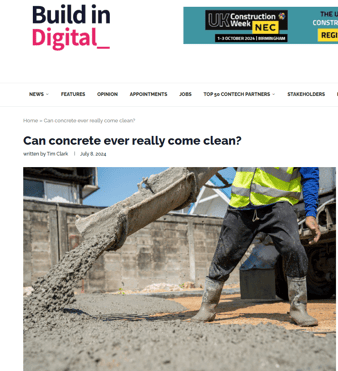
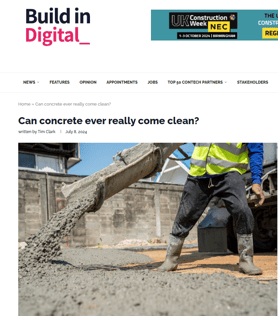
Cement and concrete are ubiquitous, but it is typically a carbon-intensive material. Undeterred, the industry is exploring ways to reduce its impact. So what is being done, how is it progressing – and can the material really clean up its act? Tim Clark reports
“For the first time in history,” the headline read, “cement production has the potential to become a net-zero industry.”
Compared to the swathe of attention that the climate emergency generates, the press release from the World Cement Association (WCA) gained little traction – at least in the UK.
Compared to the climate impact of flights to exotic destinations, concrete is rarely talked about – at least in public debate – as part of the plan to get the UK’s economy down to net zero by 2050. The material, notably cement which makes up the binding agent in concrete, is however a key part of humanity’s global carbon footprint.
The built environment accounts, by some measures at least, for up to 40% of carbon emissions. Cement production alone is over 8% of global emissions, equivalent to 2.2bn tonnes of CO2 per year. By comparison air traffic accounts for around 2% of global emissions.
“Our aim is to bring together the capabilities of cement producers worldwide with equal rights for all, regardless of size, nationality, or group,” WCA’s director, Emir Adiguzel told the body’s annual conference in China, noting how a proactive approach and investment in carbon capture technology will help bring down emissions.
“These high-cost projects signal our dedication to mitigating environmental impact and securing a greener future,” Adiguzel added. “For the first time in history, cement production has the potential to become a net-zero industry.
The estimated value of the UK’s precast concrete sector is £3.7bn, growing at around 5% per year, while the UK ready-mixed concrete sector is worth over £3bn. There are over 1,900 concrete plants in the UK supporting 29,000 employees. In the UK, concrete and cement account for 1.5% of carbon emissions, which is lower than the global average.
The government launched its roadmap to net zero in 2020. It recognises that as an industry, the UK has managed to lower its absolute carbon emissions by 53% since 1990, and has decarbonised faster than the UK as a whole.
Of course, it can be easy to decarbonise if you take the manufacturing process itself out of the UK, which is a case in many areas of the economy. The roadmap recognised this, and stated that the plan would stem any “carbon leakage” from offshoring processes that emit CO2.
Net zero journey
The journey to net-zero for concrete relies on two factors: New innovative materials that are either carbon neutral or even take carbon out of the atmosphere; and research into how to make the manufacture of traditional portland cement less carbon intensive.
In both areas, the industry itself is arguably leading the way, pulled by forward-thinking clients into new products and pushed into action by legislation.
Innovations can be categorised by a number of factors. Low-carbon cements reduce CO2 emissions during the production cycle, such as supplementing portland limestone for other materials such as fly ash or slag.
Going one step further, recycled aggregates such as recycled concrete or crushed glass again reduce the need for new materials. The next step beyond lowering the carbon content of materials is to capture the CO2 emitted from the cement process itself. Reducing the net emissions from the production process is also considered key, as is making concrete longer lasting and more durable.
Susan Bernal is professor of structural materials at the University of Leeds. In a talk outlining how the industry can reach its low carbon cement goal, she asks for the sector to be more aggressive in its adoption of new techniques, particularly when it comes to areas such as clinker replacement, or using alternative binders.
“We have many different resources which right now we consider as waste, that could be used as precursors or raw materials to develop alternative cements,” she says. “It is not about creating a new replacement to compete with cement, it’s using the chemistry of the alternative cement, to generate new routes to allow us to gain value from more of our resources.”
A spark of electro-chemistry
It is not only the materials used which can be amended. There has been progress on eliminating carbon from the cement process. US startup Chement has looked to overhaul the process by eliminating the need to heat up kilns to such a high temperature in the first place.
The firm uses an electrochemical approach to minimise the energy demands of cement production. The process uses about half the raw energy needed by the traditional technique – which requires a kiln to be heated to 1,500C. The firm claims that the process uses two gigajoules per tonne compared to four gigajoules for the standard process.
Instead, an ionisation process is used to electrochemically split calcium carbonate (CACO3), rather than heat. The emissions themselves are also purer, with the CO2 more easily captured, costing about $25 per tonne, compared to $60-$100 using traditional techniques; making the process cleaner.
A number of American firms are at the forefront of the innovations in cement production. The Decarbonisation of Cement and Concrete Alliance, known as DC2, has been formed to bring together like-minded firms in chasing the net-zero dream, and rethink production processes to develop a way to sequester CO2 directly from the concrete process.
Ten firms form part of the alliance, including Chement, Biomason, Sublime Systems, Fortera, and Brimstone.
“There is a critical need to accelerate the commercial development of deeply decarbonising technologies for cement and concrete for the sake of our climate. It is therefore inspiring to be part of the formation of DC2 along with a diverse set of companies, all across the United States, all unified with this same mission,” says Greg Houchins, chief executive of Chement.
“By working together, we can ensure that truly transformational cement and concrete technologies have a chance to scale to the point where they can realise their full decarbonisation potential.”
The UK has also a number of home-grown companies who are looking to decarbonise the concrete process.
Seratech, which is a spin-off started by Cambridge University graduates Sam Draper and Barney Shanks, has looked to utilise waste CO2 from any location – not just reduce the amount of CO2 needed – and convert it into valuable cement replacements without CO2 pipelines, shipping or oil well sequestration.
“The innovation that Seratech brings to the world is, first off, an almost zero-carbon concrete,” says Shanks. “Secondary to that it is a process which has been designed to be completely bottom up to be totally zero-waste, totally circular, and deliver a building material that people want to use that has zero carbon impact.”
Silicon dream
The firm uses waste CO2 and a form of silicon – magnesium silicate to be precise – to replace a large quantity of the aggregate in cement. The Net Zero Silica acts as a direct replacement for up to 40% of Portland cement in the concrete. Furthermore, Seratech claims that it is able to consume the emissions it creates
“We use a process called enhanced weathering, where you can grind up Olivine (a form of magnesium silicate) very fine, and transform the magnesium silicate into magnesium carbonate – and securing the carbon in there,” Shanks told the Futurebuild podcast.
The firm managed to find a way to produce a form of silica from the process that is similar to common fly ashes, which are used in concrete to reduce cracking, permeability, and bleeding.
“What we do is very similar to what happens naturally in rock, we happen to speed it up a little,” Shanks says.
According to Shanks there are enough Olivine deposits in Oman alone to be able to sequester the carbon emissions for 27,000 years – if it was utilised. The figures are astronomical, however utilising such resources at present remains an ambition more than a reality
Scales of difference
The main issue for the fledgling low-carbon concrete technologies is that the innovations aren’t – at least at present – produced on a large enough scale to make a difference.
An interim report from the Henry Royce Institute (HRI) in April this year stated that the UK will not be able to achieve its ambitions for a thriving net zero economy in the timescales demanded, “without the support of a specific, clear, and standalone national strategy for materials innovation” as well as a transition to new technology.
“It’s clear from this work that the demand for both new and improved materials must continue to increase at a staggering rate in the coming decades,” says Alan Cook, chair of the Materials Innovation Leadership Group, and David Knowles, the HRI’s chief executive.
“Now, more than ever, our drive for a more sustainable society is dependent on having the right materials at our disposal, which requires a step change in our investment.”
Draper says that government support – in the form of grants from bodies such as Innovate UK – fills a gap where venture capitalists or other investors are not keen to tread, but “there is clear potential in the idea”.
In January this year, the government’s small business research initiative (SBRI) allocated £3m to help develop low carbon concrete solutions. Individual firms could apply for up to £500,000 each to develop the material innovations further.
In terms of tackling the bigger issue on a major scale, the funding can be considered both a welcome boost and a drop in the ocean. The road to low-carbon concrete is long, however some innovative characters are treading the difficult path to a low carbon future.
Read the original article here: