Seratech in Building Magazine
The Innovations to Tackle Construction’s Carbon Problem
By Thomas Lane
8/2/20232 min read
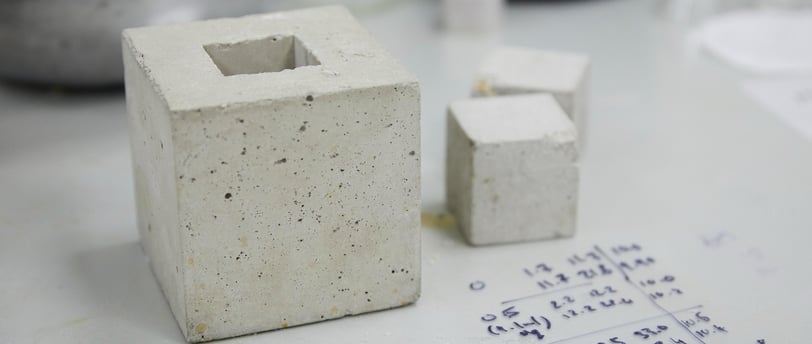
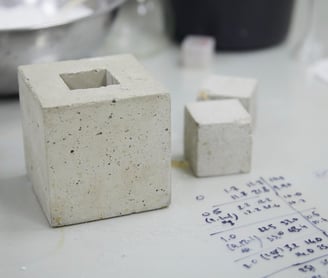
Click here for the original full length article in Building.co.uk
Watson and O’Brien are particularly excited by a product called Seratech, which came out of work done by Imperial College London. This takes magnesium silicate and combines it with CO2 to produce silica and magnesium carbonate.
“Silica is chemically very similar to fly ash and the like, so you put that in your concrete to replace a proportion of the Portland cement. It is a really familiar chemistry and gives you a concrete with good strength and durability properties,” explains Sam Draper, the CEO and co-founder of Seratech. The magnesium carbonate can be used to produce a low strength concrete for block or board manufacture.
The beauty of this process is the silica manufacture balances out the CO2 from the cement production. “The process used to produce the silica sequesters CO2,” Draper says.
“A mix that is 65% Portland cement and 35% silica is in line with existing standards for using fly ash. All the emissions from making that Portland cement is being sequestered to produce the silica which means the mix is nominally net zero.”
Draper says the testing done to date shows that the product has better early strength than concretes made using fly ash or GGBS.
The big advantage Seratech has over similar products is that it meets the chemical definition of a pozzolan, that is to say a material that does not have any cement content but behaves like one when mixed with water and Portland cement. The only difference is the silica is an engineered product, so Draper is in conversations with the Mineral Products Association and British Standards Institution to get their approval.
“Hopefully we will get a green light from them, which means it is already approved as an existing cementitious material.” And it can be used in the same way as existing concretes using the same equipment. Draper says it should cost the same or be slightly cheaper than current products as the raw materials are abundant and cheap.
The next stage is to prove the product in pilot projects with which AKTII are helping. Draper says that, once Seratech has been proven, it will put the business in a better position for getting the interest of cement manufacturers who could provide the CO2 for the process and reduce their carbon footprint.
Draper says the CO2 produced from brick kilns would also be a good source. He adds the product could be available as early as 2026, although more realistically by 2027.
Photos by Helene Sandberg