Why bury CO2 in gas fields? Use it to build!
By Natasha Higgins
6/26/20244 min read
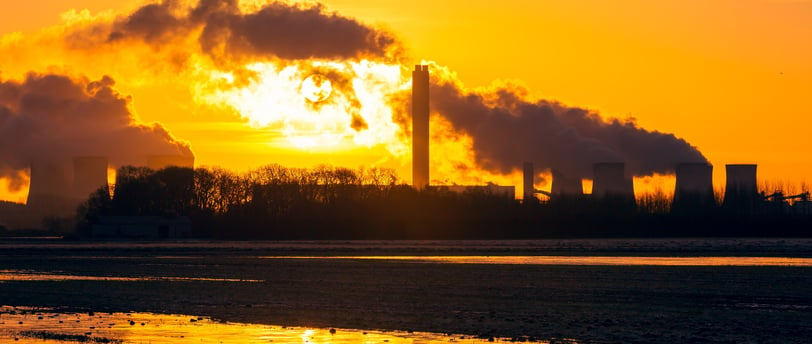
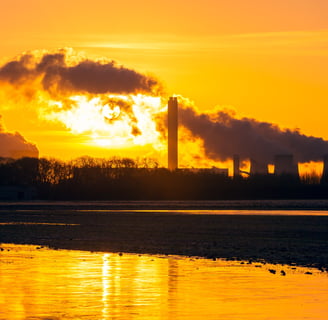
Huge efforts are underway to decarbonise ‘hard to abate’ industries and carbon capture technologies are set to play a key role whether CO2 is pumped underground or used to make new building materials as in Seratech’s process.
Seratech’s process is unique as it captures CO2 and mineralises it into materials that replace cement in building materials. Not only is the CO2 mineralised permanently but the resulting products replace cement thus avoiding further emissions.
The cement industry alone is responsible for 8% of annual global CO2 emissions and while progress is being made to remove CO2 from the cement making process by decarbonising the grid, using biomass and supplementary cementitious materials, according to Mike Eberlin, Seratech’s non-executive director and former MD of Tarmac Cement & Lime, there is still a remaining ‘lump’ constituting 60 to 65% of emissions that will have to be dealt with using Carbon Capture.
Most experts will agree that a range of different solutions are needed to combat climate change seen as the largest global technological challenge of the century. However, CCS (Carbon Capture and Storage) has been at the forefront of the debate for some time due to the controversial nature of burying CO2 and the worry that it will allow us to continue burning fossil fuels as we have done for the past 100 years. While a small amount of carbon capture either as a temporary measure or as a way of addressing hard to abate industries is unavoidable, there needs to be real technological change and paradigm shifts.
As the debate rages on, 41 CCS projects are now in operation globally and another 351 are in development according to The Global CCS Institute. Canada’s Wolf Alberta Carbon Trunk Line (ACTL) is leading the way with the ultimate capacity to deliver 14.6 million tonnes of CO2 per year to permanent storage.
“When we talk about CCS as opposed to CCMU (Carbon Capture Mineralisation and Utilisation), we are referring to capturing and storing CO2 underground as a waste product, in depleted gas and oil fields versus capturing CO2 and using it for novel applications like building materials – as a way of getting it out of the atmosphere,” explains Sam Draper, Seratech CEO.
“The issue with CCS is that it relies on a new set of logistics and high-level investment. Cost remains the biggest single barrier with most European CCS projects requiring very large EU or Government subsidies to get going. These projects also require huge amounts of energy to capture, transport, purify and liquify CO2 geologically which is going to be inherently expensive,” he explains.
Professor Martin Blunt, at Imperial College London, has been studying CCS for over 20 years and remains a strong advocate for the technology but does not underestimate the huge implementational challenges it brings with it.
“The reality is that if we want to reduce CO2 at gigaton scale the only feasible option is to inject a vast amount underground. There is growing appreciation that CCS is a vital component of decarbonising industry. While it’s a challenging one, it's the only challenge intrinsic to preventing dangerous climate change and living in an advanced economy.
The main obstacles associated with CCS for now are scale, cost and the need to lay pipelines for CO2 transportation: “To make a big difference to climate change we need to ramp up storage significantly and figure out how to create an economic model that makes it beneficial to use.
“In the UK we have two industrial clusters going ahead and we are fortunate to have our heavy industry located near saline aquifers i.e. coastal storage sites notably Liverpool Bay and The North Sea. The UK alone will be responsible for tens of megatons of CO2 storage otherwise it becomes unclear as to how we can continue to have heavy industry”.
While Eberlin agrees that for plants that already sit next to oil and gas fields it’s acceptable to capture and pump their CO2 underground, he points out that a lot of heavy industry in Europe and the USA is nowhere near gas fields and believes it’s simply too expensive to lay new pipelines around countries. He further adds that CCS more than doubles the costs of a cement plant on a capital and operating basis.
“CCS is a cost drain process for industrial emitters which is why alternatives such as Seratech’s CCMU process, which not only uses a cement replacement in the form of silica but also captures the remaining CO2 and mineralises it into new building products generating a new revenue source for emitters, is an attractive option. For 1 tonne of CO2 absorbed we generate over 3 tonnes of products which replaces around 3 tonnes of cement avoiding an additional 2 tonnes of CO2 emissions,” explains Eberlin.
A common problem across all these technologies is the genuine frustration at the slow pace of development mainly due to the lack of legislative commitment. Most of these engineering challenges were identified 20 years ago according to Blunt: “The separation of CO2 from flue gases has been around for almost a hundred years and the storage of those gases has been standard since 1970. Norway was the first project and has been a success for well over 20 years – we know we can do it, but implementation is slow”.
While implementation may be lagging, latest figures show that on average 1 to 2bn Euros of public funding is being pumped into each CCS hub. There are currently five CCS hubs across Europe in development in Norway, The Netherlands, France and the UK in a bid to reach net zero by 2050.
“We have 25 years to decarbonise our economy and it’s the biggest challenge facing us,” concludes Eberlin. “We’re fortunate to have some brilliant technologies out there and as most people will say, in order to reduce the 40bn tonnes of CO2 we emit annually, we will need to rely on everything we can from mineralising CO2 to pumping it underground”.